CLT - Cross Laminated Timber
- Aakarsh singhal
- Oct 29, 2016
- 4 min read
Cross-laminated timber (CLT) is a plate-like product made from timber. Layers of planks are glued orientated at 90° to each other, usually in a symmetric way so that the outer layers have the same orientation. An odd number of layers is most common but there are configurations with even numbers as well (which are then arranged to give a symmetric configuration). The cross gluing allows using the plates with two span directions whereby some differences in stiffness and strength are observed along the two directions. It is similar to plywood but with distinctively thicker lamination.
Cross-laminated timber is fast establishing itself as a quicker, greener alternative to concrete or steel structural frames. With the market growing threefold in the past two years, is it time to consider it a genuine rival to the big two?
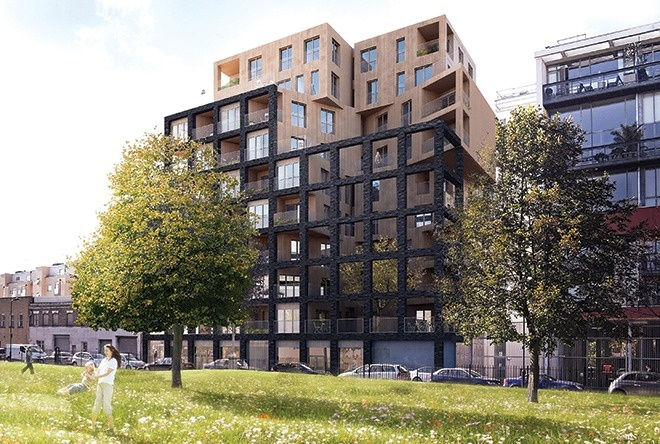
These panels are available in a variety of sizes, are great for building entire structures, including internal walls and floors, very quickly. The lightweight nature of the material means foundations can be smaller and cheaper, it is clean to use, with little waste, and it is made from readily available, renewable softwoods, which makes achieving high BREEAM (Building Research Establishment Environmental Assessment Methods) ratings easier, and looks good in the corporate sustainability report.
Moreover, while most of the noise around modern methods of construction is concentrated on low-rise buildings, the height of CLT buildings is creeping up. Two years ago developer Lend Lease completed a 10-storey residential block in Melbourne, the world’s tallest CLT project to date, and now engineer Ramboll is working on the structural design of two 10-storey residential buildings in the UK.
“Housebuilders and developers are waking up to the fact they can get their building up and get their money back faster [by using CLT].”
CLT was going to be used for part of the structure of the stalled Google HQ in King’s Cross, London. The plan was to use a primary steel floor structure infilled with CLT panels sitting on the lower flange of the steel I beams. This would have supported raised access flooring, with the finished floor sitting just above the top of the steel beams.
One of the biggest barriers to the march of CLT could be skills shortages in a resurgent economy. “It is very hard to find good structural engineers with timber experience,” says White. “If more people were coming out of university with timber experience you would see it being used more.”
The speed test
One of the great advantages of CLT is its speed of construction. The panels are made to measure in the factory, complete with openings for doors and windows. This means that lead-in times are longer - typically 12 weeks from scheme design to the panels arriving on site - but after that, things move fast.
John Mills, construction manager for Lend Lease, is overseeing the construction of Trafalgar Place, the first phase of the Elephant and Castle regeneration. This consists of seven apartment blocks containing 235 flats. Two blocks containing 30 apartments are being built from CLT, and Mills is already a convert. “It’s so much quicker, cleaner and less hazardous than concrete,” he says. “Only eight men were needed to construct this block rather than 60 or 70 if we had used concrete.”
Mills says the first CLT block took 12 weeks to construct compared with 20 weeks for concrete, and adds that it should have taken just seven weeks but not enough crane time was allocated to the job. The crane was shared with the concrete team and there were issues with wind. “Next time the CLT erectors will have a dedicated crane,” Mills says.
The panels arrive ready to crane into position and are simply screwed together. “With concrete you need carpenters to build the shuttering and more men to put in the rebar, pour the concrete and strike the shuttering,” Mills says. “And there is a five-week propping regime while it cures.” With CLT, follow-on trades can start work as soon as each floor is completed.
There are further time-saving benefits to CLT. The panelised nature of the material eliminates the need for lightweight steel framing systems to close in the building perimeter. And fixing materials to the structure is much easier as workers can quickly drill holes and insert screws. The speed of fixings could yield further cost savings, helping Lend Lease to tip the financial scales further towards CLT. “We are looking for savings; there are benefits for the supply chain and benefits for us,” says Lend Lease project manager Martyn Fennell. “It could also make it easier to get trades as demand picks up.”
Drilling into concrete is noisy and dusty and requires a special fixing. “There is no hazardous silica dust which is the second biggest killer on sites,” says Mills, adding that, unsurprisingly, this makes CLT very popular with workers.
CLT is claimed to be as strong and fire-resistant as structural steel or concrete. In 2016 plans were proposed for a 40-storey CLT building in Stockholm and a 100-storey tower in London.
In September 2016 the world's first timber mega-tube structure was built at the Chelsea College of Arts in London, using hardwood CLT panels. The 115 feet (35 m) long "Smile" was designed by architect Alison Brooks, in collaboration with the American Hardwood Export Council, for the London Design Festival.
Comments