Stadthaus
- Aakarsh singhal
- Nov 15, 2016
- 3 min read
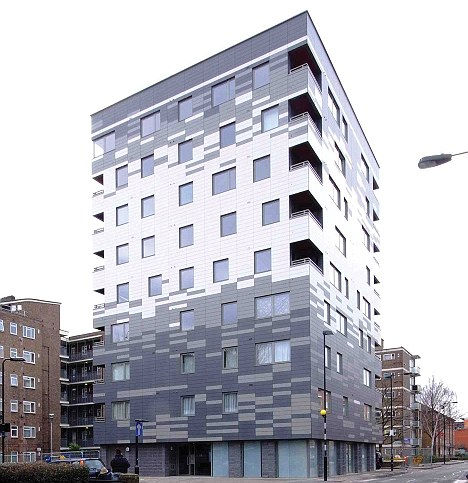
Stadthaus, Murray Grove
Project Detail
Project Value: Confidential
Project Dates: 2007 - 2009
Services: Supply and Erect
Timber Vol. : 926m3
Build Period: 7 weeks
Design Team
Architect: Waugh Thistleton
Engineer: Techniker
Client/Contractor: Telford Homes
Its gray and white facade blends almost seamlessly into the overcast London skies. It’s what’s inside that makes Stadthaus stand out. Instead of steel and concrete, the floors, ceilings, elevator shafts, and stairwells are made entirely of wood.
But not just any wood. The tower’s strength and mass rely on a highly engineered material called cross-laminated timber (CLT). The enormous panels are up to half a foot thick. They’re made by placing layers of parallel beams atop one another perpendicularly, then gluing them together to create material with steel-like strength. “This construction has more in common with precast concrete than traditional timber frame design,” Thistleton says. Many engineers like to call it “plywood on steroids.”
CLT since then...
When it opened in 2009, Stadthaus was by far the world’s tallest modern timber building. Since then, CLT towers have sprouted up everywhere. Waugh Thistleton built a seven-story apartment tower near Stadthaus in 2011, and construction is under way on a 90-foot-tall wood building in Prince George, British Columbia. In 2012, Stadthaus lost the height record to a 10-story apartment building in Melbourne called Forté.
There are plans to go even higher. Swedish authorities have approved a 34-story wood tower in Stockholm, while Michael Green, a Vancouver architect, is seeking approval for a 30-story tower in his city. And the Chicago architecture mega-firm Skidmore, Owings & Merrill recently published a feasibility study for a 42-story tower made predominantly of CLT. It’s become a competition among architects to see who can build the next tallest wood high-rise, says Frank Lam, a professor of wood building design and construction at the University of British Columbia.
Construction
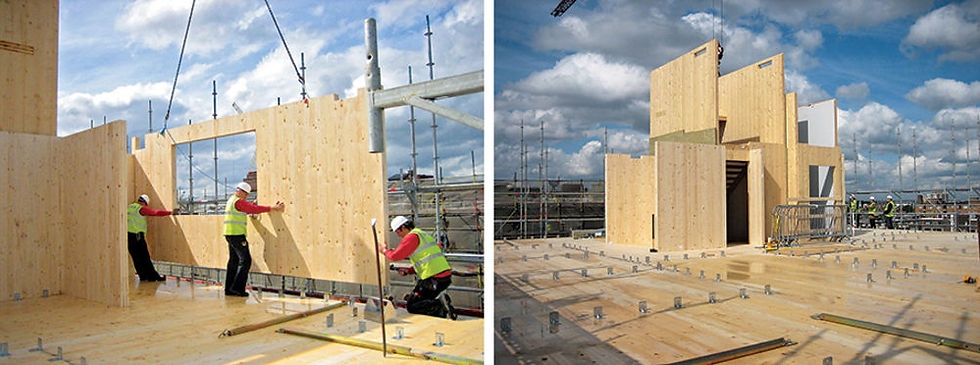
Wood, on the other hand—even engineered wood like CLT, which requires additional energy to cut and press into sections—is far more environmentally friendly. According to Wood for Good, an organization that advocates for sustainable wood construction, a ton of bricks requires four times the amount of energy to produce as a ton of sawn softwood; concrete requires five times, steel 24 times, and aluminum 126 times. Wood also performs better: It is, for example, five times more insulative than concrete and 350 times more so than steel. That means less energy is needed to heat and cool a wood building.
The process for producing cross-laminated timber makes clear why architects call it “plywood on steroids.” Its layered structure gives it immense strength in two directions, producing a lightweight alternative to steel or concrete.
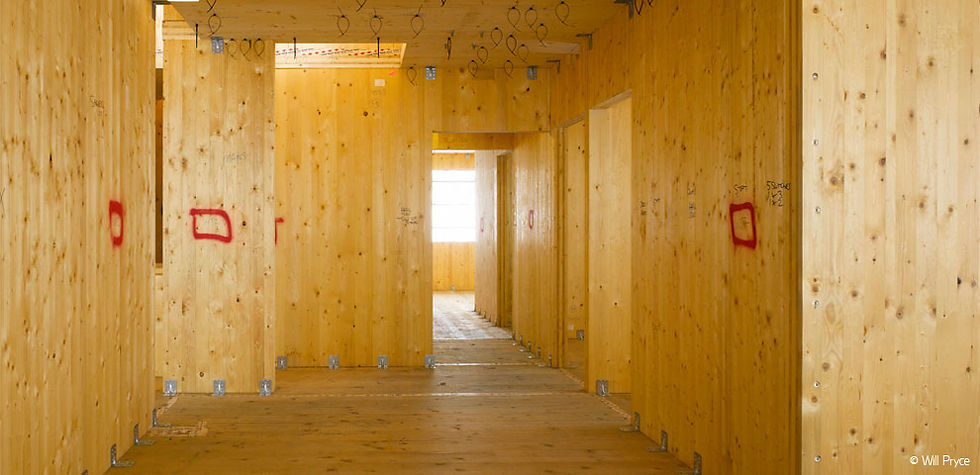

Anatomy of a Timber Tower

1) Whereas steel or concrete structures are skeletal, using columns to carry loads, CLT towers distribute weight over the entire, solid vertical panel.
2) Steel or concrete L-brackets fix the horizontal and vertical CLT panels together.
3) The horizontal spans between vertical CLT elements can be significantly longer than with steel or concrete beams.
4) Interior walls are usually fireproofed by applying a layer of gypsum paneling on top of the mass timber panels.
5) A two-inch layer of concrete typically covers two two-inch layers of insulation (separated by a three-inch void) to reduce acoustic vibration between floors.
6) Panels come made to order with windows cut out and sometimes piping and electrical installed. Construction is as easy as screwing the panels together.
7) Elevators have double walls with insulation sandwiched between them for fire safety and soundproofing.
Comments